Poly Shape
The Poly Shape in CabMaster is a versatile machinable part that can be customised to almost any shape, and also have a range of different cutouts applied to it:
- Circles
- Drill Holes
- Routes
- Cutouts (X & Y coordinates)
- Cutouts (Size & Position)
This document will detail each page of the Poly Shape’s options and how they can be applied to your drawing.
Cabinet Details: General
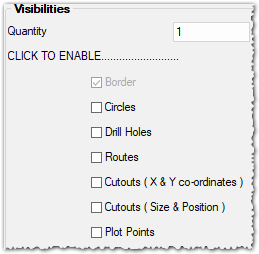
This is the first page that you see when you open the Poly Shape. It gives the initial setup options for what you would like to do for the inner part of the Poly Shape (“Visibilities”), as well as providing options of how you would like to edit the part (“Border Style”).
Visibilities
Circles: A circle cutout at a specified position on the part. Example usage: Hole for electrical wires.
Drill Holes: Repeatable straight lines of drill holes. Example usage: Continuous shelf holes.
Routes: Straight lines that can be routed. Example usage: Air vents.
Cutouts (X & Y coordinates): Using up to 10 plot points, for creating a cutout in the part by the X & Y coordinates.
Cutouts (Size & Position): Create 4-sided shapes to be cutout in the part by provided the size and position of the cutout.
Plot Points: This does not create any shape on the part, but simply shows the direction which you would plot each point to create your desired shape.
Selects whether the poly shape will be made out of carcass or panel material.
Border Style
Standard: Sets the poly shape to be a simple square or rectangle, with the size of the part specified on the Border page. As the part will have 4 flat sides, the option of edging each side is enabled.
Advanced: Specifies that the poly shape will be created by using up to 20 plot points, with the added option of applying radiuses.
DXF: Gives the option of setting the poly shape to be the same shape provided by a DXF file. The DXF file is selected on the Border page.
Cabinet Details: Border
When Standard or DXF are selected in the Border Style section above, this page provides is where you set the size of the part, specified as Height and Width values. You can give a name for the Layer that will be used for the Border in a nesting program (eg, EzyNest) if ‘Border’ is not suitable.
As shown in the image below, to enable a row to be edited, turn on the checkbox on the right side of that row. Only turn on the checkboxes for the rows that you require to be used.
When Advanced is selected as the Border style, the method of setting the size of the part is very different. As shown in the image above, it uses X & Y coordinates with the additional option of applying a radius to each corner. This example above is also using the option of Plot Points as selected in the Visibilities section.
NOTE: X refers to the horizontal plane (left/right), whereas Y refers to the vertical plane (up/down).
To provide plenty of versatility, there are 20 plot points available, with 12 on the page Border, and an additional 8 on the page Border ct’d.
The above image shows a random shape created using 7 plot points. Normally Point 1 will begin at X:0mm and Y:0mm as shown above, with all subsequent points being defined in a clockwise direction.
Also note that each plot point is an X/Y coordinate as measured from the X:0mm Y:0mm position.
The third column is to specify the radius to be applied to the corner. Most of the time this will be a positive value, but as indicated above, in this example Point 5 is a negative value as the radius is curved inwards instead of curved outwards (compare with Point 2).
Cabinet Details: Border ct'd
This page contains more available X/Y coordinates (Points 13 to 20) to create your shape, if required. On this page you will also see the Layer and Offset options. Layer is the layer name that will be used for the Border of the Poly Shape in a nesting program (eg, EzyNest). This is recommended to be set to ‘Border’ but can be changed if required.
The Offset option creates a duplicate of the Border that is smaller by the Offset value. As shown in the example below, the Offset is set to 60mm, so the Border has been duplicated on the inside of the shape. This gives the effect of a frame, where the inner border will be cut out.
Cabinet Details: Circles
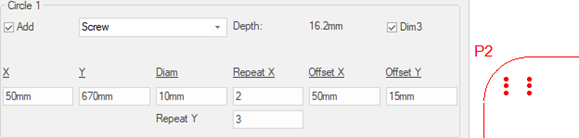
This page gives the option of 3 sets of circles cutouts to be applied to the shape. Turn on the checkbox marked Add, and all the other options as shown will appear. In the example above, the Layer name is ‘Screw’, and the Depth is set to 16.2mm. As the Dim3 checkbox is ticked, this value is automatically set to the material thickness (here it is 16.0mm carcass) plus the value shown in Drawing Properties à Mach.General à Tool2 à All Others:Other Material (in this example it is 0.2mm). If the Dim3 checkbox is unticked, a textbox will appear that gives you the option to enter your own value to define the cutting depth for the circle.
The position of the initial hole is X:50mm Y:670mm, shown above in red as the bottom left hole, with a Diam (diameter) of 10mm. Repeat X here has been set to 2, which creates 2 holes separated by the value entered in Offset X. Additionally, as Repeat Y has been set to 3 and Offset Y has been set to 15mm, there will be 3 holes vertically that are measured 15mm apart.
Cabinet Details: Drill Holes
Whereas the Circles page is intended for creating individual [or a small number of repeated] holes, the Drill Holes page is specifically intended for creating at least 2 rows of repeated holes. An example of this option is to make continuous shelf holes.
The options on this page are mostly the same as for the Circles page. The X:Start specifies the distance of the holes from the left edge (measured from the 0mm mark), and the Y:Start specifies the distance that the holes will start from the bottom edge (also measured from the 0mm mark). X:End is the position of the right column of holes measured from the left edge, and Y:End is the position of the right column of holes measured from the bottom edge.
If you were to turn on the checkbox marked Extra Rows, a third column of holes would now be present, measured in the exact centre between the two existing columns. Changing this value will add more columns of holes, each evenly spaced between the initial left & right columns of holes.
Cabinet Details: Route
The Route page provides the option of multiple straight lines to be routed in the poly shape.
The Route lines are positioned by the X:Start and Y:Start values, measured from the bottom left corner, and continue in a straight line to the location specified by the X:End and Y:End values. The number of lines is specified by the Repeat value and are offset by the Repeat X and Repeat Y values. Again, all values are measured from the X:0mm and Y:0mm positions.
As shown in the example above, the bottom route line starts at 50mm from the left edge and 80mm from the bottom edge. The line continues towards the right until it reaches 325mm from the left edge and 150mm from the bottom edge. This line is repeated 18 times, with each line positioned a further 5mm from the left edge, and a further 32mm from the bottom edge. Each line will be routed as 13mm deep (unticking the Dim3 checkbox provides the option of specifying a routing depth) and will be nested using the layer name ‘Cut’.
Cabinet Details: Cutout1, Cutout2, Cutout3
Cutout1, Cutout2
Cutout1 and Cutout2 are identical, providing two iterations of the same option. Cutout3 provides alternative measurement options which will be covered later in this document.
Looking initially at the bottom left of the 6 cutouts, this is set up in the same style as the Cabinet Details à Border page, which uses X/Y coordinates to position each corner of the cutout shape.

NOTE: AN outward-curved radius requires a positive value, and an inward-curved radius requires a negative value.
This bottom left cutout starts at 100mm from the left and 400mm from the bottom and applies a 25mm outward-curved radius. The second point is also measured 100mm from the left edge and is 400mm from the bottom edge. The third point is 200mm from the left edge and 400mm from the bottom edge, with a 25mm inward-curved radius (requiring a negative value for the radius). The fourth point is 200mm from the left edge and 350mm from the bottom edge.
A Repeat X of 2 has provided 2 columns of this same cutout shape, measured 225mm (Offset X) from the left edge of the bottom left cutout. Similarly, a Repeat Y of 3 has set this to have 3 rows of this same cutout shape, measured 150mm (Offset Y) from the bottom edge of the bottom left cutout.
NOTE: The X and Y coordinates of the Points values are measured from the bottom left corner (X:0mm and Y:0mm) of the poly shape. The Repeat's Offset X and Offset Y values are measured from the bottom left corner of the cutout shape that has been created by using the Points values (the exact position which is X and Y in the Point 1 row).
Cutout3
The Add, Layer, Depth/Dim3, and Repeat options on this page work the same as on the other pages as detailed above.
This page provides a different method of creating a cutout in your poly shape. The Width (shown below as 200mm) and Height (250mm) values specify the size of the cutout. The Chamfer (50mm) is the size of the chamfered corner to be applied (when the option is selected for that corner, more on that later).
The checkbox to the right of Chamfer is to invert the radius. As shown in the cutout below, the upper left corner has an inward-curved radius. If this checkbox was unticked, it would show an outward-curved radius instead.
The Measure to Centre checkbox sets the origin point of the cutout to the centre of the cutout. This would make the Vertical Distance and Horizontal Distance measure from the centre of the cutout. Alternatively, the Measure to Corner will set the origin point to the bottom left corner of the cutout shape. As shown in the example above, the cutout shape is being measured from is bottom left corner and is 400mm from the bottom edge of the poly shape and 120mm from the left edge.
The checkboxes at the bottom are for enabling the chamfer and radius for each individual corner of the cutout. Don’t be worried by what looks like random letters – BL is Back Left (Top Left), BR is Back Right (Top Right), FL is Front Left (Bottom Left) and FR is Front Right (Bottom Right).
In this example above, the Back Left and Front Right have the chamfer turned on. In addition to the chamfers, the Back Left also has the Radius enabled.
Labour & Construction: Options
Orientation: Specifies whether the poly shape will be positioned in your drawing as Flat (shown in Plan View as its shape, similar to a benchtop) or Vertical (shown in Plan View similar to an End Panel).
Height Off Floor: If your poly shape will be viewed in 3D View, here you can specify the distance that the part will be positioned above the floor.
TIP: Click the attachment to download this HowTo to your desktop as a .pdf